Definition of insulated glazing
Insulated glazing consists of two or three glass panes separated by an insulating spacer with a sealed gap, called a cavity, between the panes. This gap is often filled with air or an insulating gas to enhance the thermal performance of the glass unit.
This unit improves thermal efficiency by reducing heat transfer and helps retain heat in winter and blocks heat in summer.
Advanced technologies like Low-E coatings and inert gas or vacuum make insulated glazing much more efficient than traditional single glazing.
History of insulated glazing in the UK
Insulated glazing originated in the 1930s in the United States, it was adopted in the UK in the 1970s. Before then, homes were mostly single-glazed, which offered poor insulation.
The 1973 oil crisis increased the demand for energy efficiency, and double glazing became common in new builds and retrofits.
Over time, UK building regulations implemented minimum thermal efficiency standards, leading to the widespread adoption of insulated glazing.
Generation and evolution of insulated glass
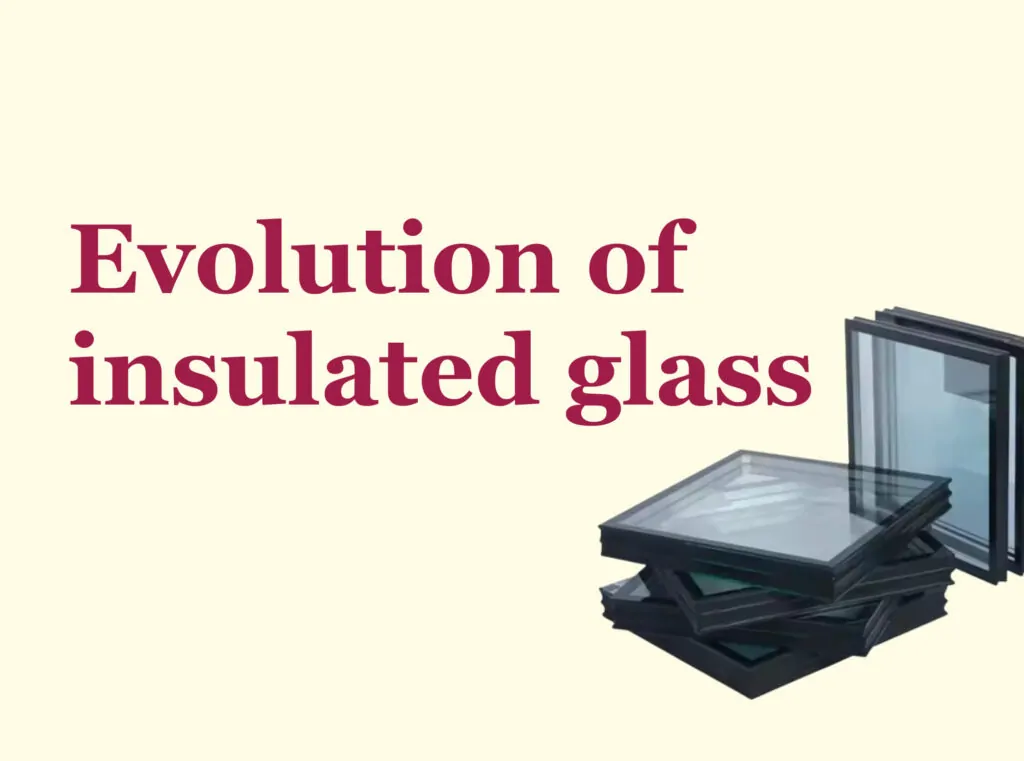
Double glazing with air-filled cavity – 1930s
Double glazing with air-filled cavities was developed in the 1930s and registered under Thermopane trademark in the United States to improve insulation and reduce heat loss through windows.
It was designed to provide better thermal efficiency than single glazing, especially in cold climates.
Double glazing and triple glazing with gas-filled cavity – 1970s
In the 1970s, gas-filled cavities became a key advancement in insulated glazing. Manufacturers began using gases such as argon, which are denser than air, to improve thermal performance.
Gas filling significantly reduced heat transfer and made both double and triple glazing more effective at insulating homes.
Different glass thickness for better sound insulation – 1980s and 1990s
Using different thicknesses of glass panes in a single insulated unit to improve sound-proofing performance became popular in the 1980s and 1990s, especially in urban environments like cities or near airports.
With different thicknesses of the glass panes, windows could block a wider range of sound frequencies, greatly improving noise reduction.
Double glazing and triple glazing with Low-E glass lamination – 1990s
In the 1990s, US company Southwall Technologies released Low-E (Low-Emissivity) glass.
Low-E coatings on double and triple glazing further improved their insulating properties reflecting heat back into buildings while still allowing natural light transmission.
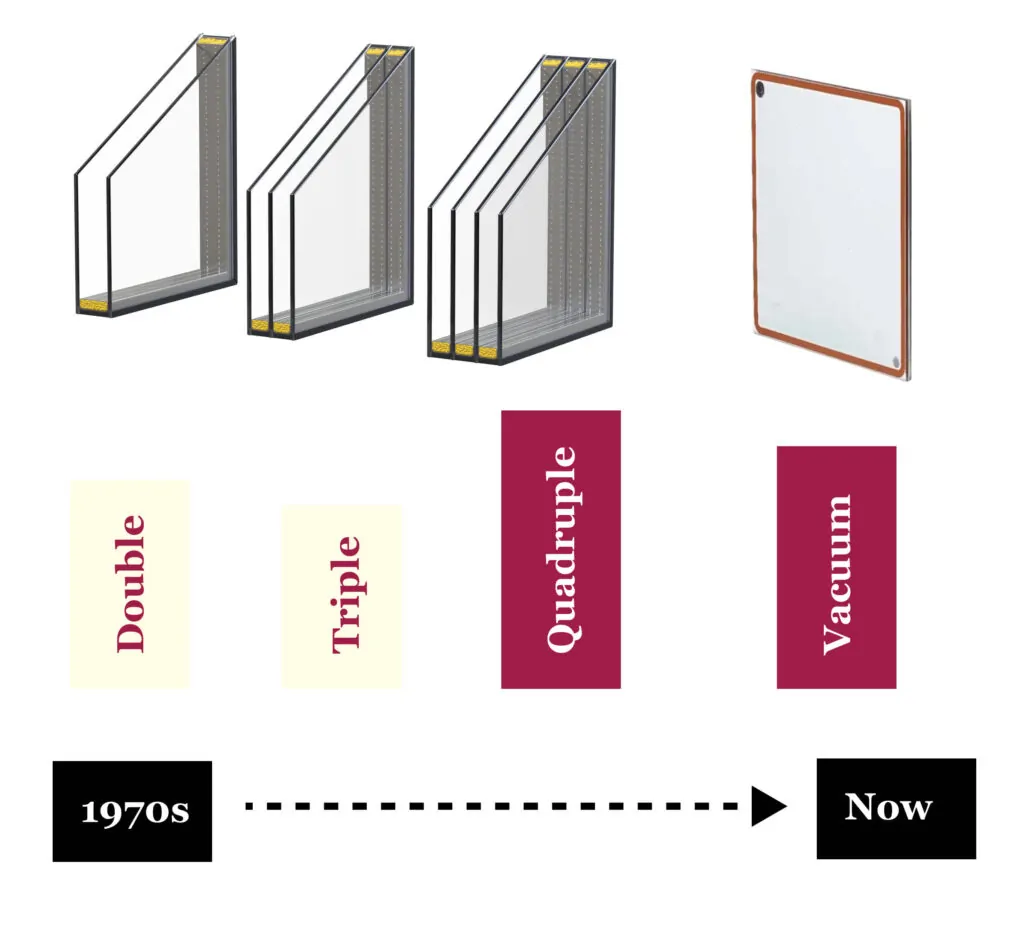
Quadruple insulated glazing – early 21st century
Quadruple glazing was developed in the early 21st century in response to the need for even greater thermal efficiency, particularly in extremely cold climates. It consists of four panes of glass with three gas-filled cavities, providing exceptional insulation with very low U-values.
However, due to its increased thickness, weight, and cost, quadruple glazing remains less common than double or triple glazing and is generally used in specialised projects like passive houses or zero-energy buildings.
Vacuum insulated glazing with Low-E – 21st century
Vacuum insulated glazing (VIG) was first developed in the late 1990s by Nippon Sheet Glass (NSG).
Their product, Pilkington Spacia, became the first commercially available VIG unit. VIG was designed to provide superior thermal insulation with a slim profile, ideal for retrofitting into heritage properties.
Since then, other companies like LandVac and Fineo have further refined vacuum glazing technology, enhancing its thermal performance, adjusting the design and expanding its use.
VIG units use a vacuum gap and Low-E coatings to achieve high insulation levels with minimal glass unit thickness, making them one of the most efficient modern glazing options.
How insulated glass thermal efficiency is measured
U-value and R-value
The thermal efficiency of insulated glass windows is most commonly measured using two metrics: U-value and R-value.
Both of these metrics are important for understanding how well a window prevents heat loss, although they represent this efficiency in slightly different ways.
R-value of insulated glass
R-value indicates how the material resists heat flow. A higher R-values mean better resistance to heat transfer, and therefore, better insulation.
In the context of insulated glass, the R-value indicates how much heat the window unit can keep from escaping your home.
A higher R-value means higher insulation, which helps minimise the need for additional heating or cooling.
Although R-values are commonly used to measure the thermal resistance of insulation materials in walls, roofs, and floors, they still provide a useful reference point when comparing the insulating properties of different glass types.
U-value vs. R-value: key differences and their importance
The U-value shows how much heat passes through the glass. Lower U-values mean that a lower amount of heat can be lost through the glass resulting a better insulation.
In the UK, the U-value is the main metric for measuring energy efficiency, as it determines how well the insulated glass unit retains heat.
Here is a comparison of typical U-value and R-value ranges for different types of glazing:
Type of glazing | U-value (W/m²K) | R-value (m²K/W) |
Single glazing | 4.5 – 5.8 | 0.17 – 0.22 |
Double glazing | 1.2 – 3.0 | 0.33 – 0.83 |
Triple glazing | 0.6 – 1.0 | 1.0 – 1.67 |
Vacuum Insulated Glass | 0.4 – 0.7 | 1.43 – 2.5 |
As can be seen from the table shows, single glazing provides poor thermal insulation with high U-values and low R-values.
Double glazing and triple glazing provide better performance, while vacuum insulated glass (VIG) is the most thermally efficient option, with the lowest U-values and the highest R-values.
In practice, the U-value is the standard measure for windows and glazing units, as it clearly reflects the window’s ability to prevent heat loss.
For optimal thermal efficiency, choose insulated glazing with a low U-value and a high R-value.
Components of insulated glass
Types of insulated glass
Toughened glass
Toughened glass, also called tempered glass, is manufactured by heating regular glass to a high temperature and rapidly cooling it down.
This process makes the toughened glass much stronger than standard glass and more resistant to impacts and sudden temperature changes.
If tempered glass breaks, it splits into rounded pieces instead of sharp shards significantly lowering the injury risk.
Float glass
When molten glass is poured on a bed of molten tin, it creates a float glass – a perfectly smooth and even glass surface with consistent thickness and clarity.
This method is the standard process for manufacturing high-quality glass. Float glass is frequently used in double glazing and can be further treated for enhanced properties, such as energy efficiency or soundproofing.
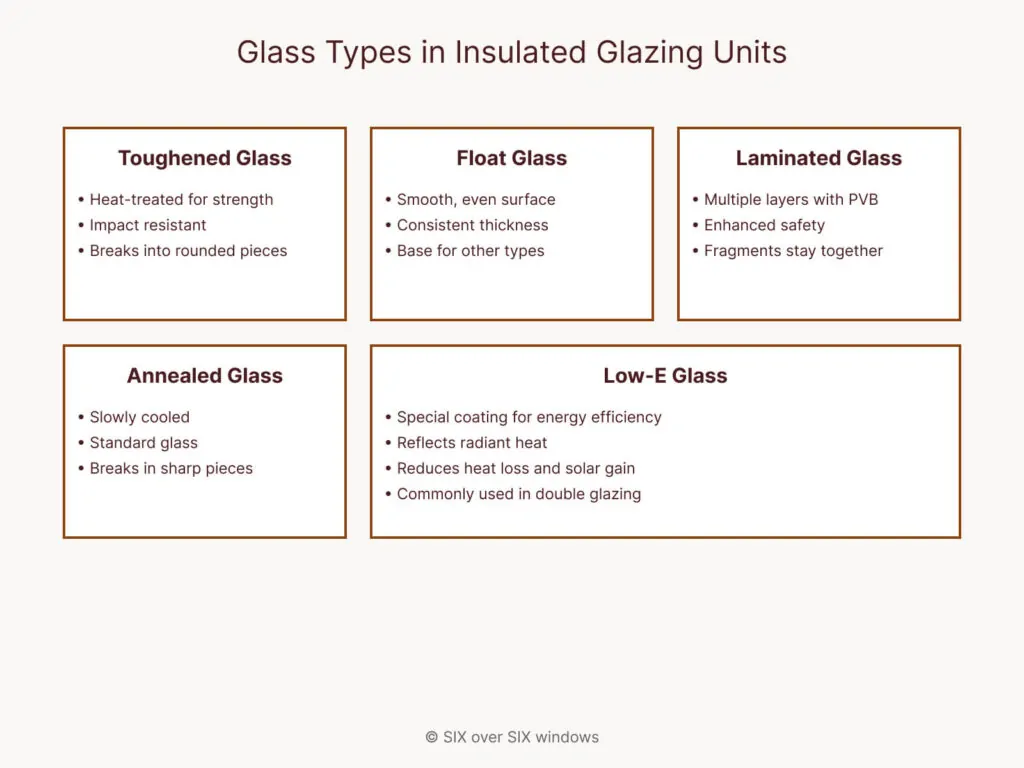
Laminated glass
Laminated glass is produced by bonding of two or more glass layers with a plastic interlayer, typically PVB (polyvinyl butyral) creating a strong and durable sheet that enhances safety, security and soundproofing.
In case of destruction, glass fragments stick to the interlayer, which prevents them from scattering.
Annealed glass
Annealed glass is a regular glass that has been cooled slowly to relieve residual stress in the glass. It is weaker than toughened or laminated glass and breaks into sharp pieces.
Low-E glass
Low-E (Low-Emissivity) glass is covered with a thin coating usually on the inner surface of the outer pane.
It allows natural light to enter but reflects radiant heat, enhancing thermal insulation and energy efficiency.
Low-E glass is commonly used in double glazing to enhance energy efficiency by reducing heat loss in cold weather and minimising solar heat gain in hot weather.
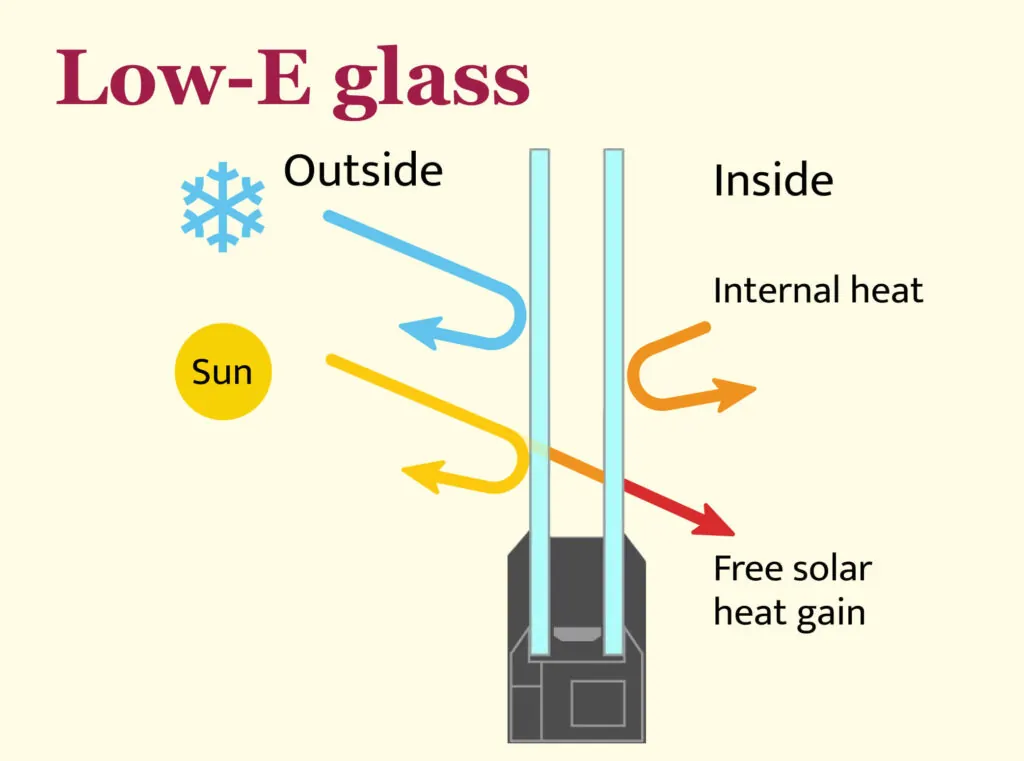
Wired glass
Wired glass has a mesh of thin metal wires embedded within the glass, primarily used for fire resistance. It is not commonly used in traditional residential double glazing but can be incorporated into fire-rated double glazing systems for areas requiring fire safety, such as doors or windows in commercial buildings.
Patterned or textured glass
Patterned glass has a texture or pattern imprinted during manufacturing. This design ensures privacy while still allowing light to pass through.
It is commonly installed in bathrooms, offices, and other areas where privacy is important, often combined with a second clear glass pane for better insulation.
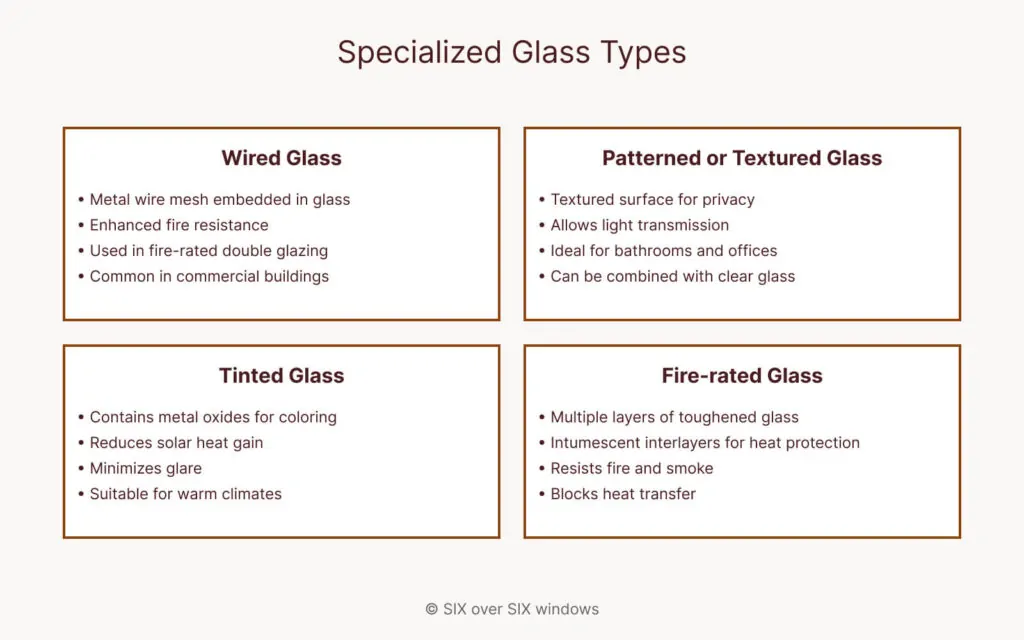
Tinted glass
Tinted glass is a glass with colored appearance thanks to adding metal oxides and colour additives during production. It is often used in double glazing units to reduce solar heat gain and glare, making it ideal for warmer climates or for buildings where aesthetic appeal and solar control are priorities.
Fire-rated glass
Fire-rated glass, also known as fire-resistant glass, is constructed from multiple layers of toughened glass combined with intumescent interlayers that expand when exposed to heat, providing enhanced fire protection and safety. It was specifically designed to resist fire, smoke, and transfer of radiant and conductive heat.
Films & coatings
Standard clear glass has been the primary option for many years, but more advanced glass types such as Low-E glass (low-emissivity) are commonly used today to achieve optimal thermal efficiency.
Low-E glass with a microscopically thin coating was designed to reduce the amount of light (infrared and ultraviolet) passing through the glass without affecting the amount of visible light that penetrates.
In winter, the Low-E glass coating reflects heat back into the room, keeping the home warmer, and in summer, it reflects the sun’s heat, helping to keep the home cooler.
Low-E glass greatly improves the insulation of windows. As a result, your energy bills become lower because you reduce the need to use constant heating in winter and cooling in summer, which lowers energy costs.
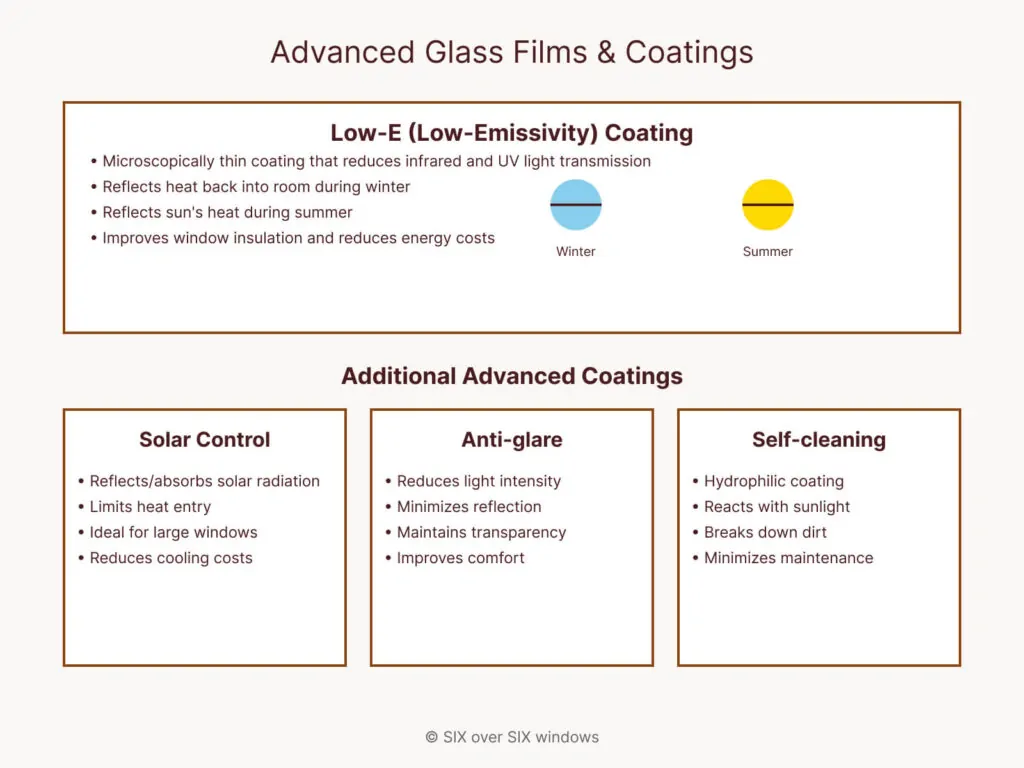
In addition to low-emissivity coating, several other advanced coatings help to improve the overall performance of insulated glass units:
- Solar control coatings are specifically engineered to reflect or absorb solar radiation, limiting the amount of heat that enters a building which is ideal for properties with expansive windows or in regions with intense sunlight. By reducing solar gain, these coatings help lower cooling costs in summer and minimise glare, making indoor spaces more comfortable.
- Anti-glare coatings are often used in environments where large amounts of natural light enter a room. They reduce the intensity of light and reflection, making space more comfortable without darkening the room or reducing transparency.
- Self-cleaning coatings have a hydrophilic layer that reacts with sunlight on the glass surface and kills dirt and organic matter on the glass surface. This process allows rainwater to easily rinse away the loosened debris, keeping windows cleaner for longer periods with minimal maintenance.
Insulated glass units can be tailored to suit specific needs, whether it’s reducing glare, controlling solar heat gain, or reducing maintenance costs.
Spacer systems
The spacer is a material that separates the panes of glass, creating a sealed cavity between them, which is crucial for improving thermal insulation.
Spacers were designed to hold the glass sheets apart at a precise distance to form airtight seal edges, maintaining the integrity of the gas or air within the cavity.
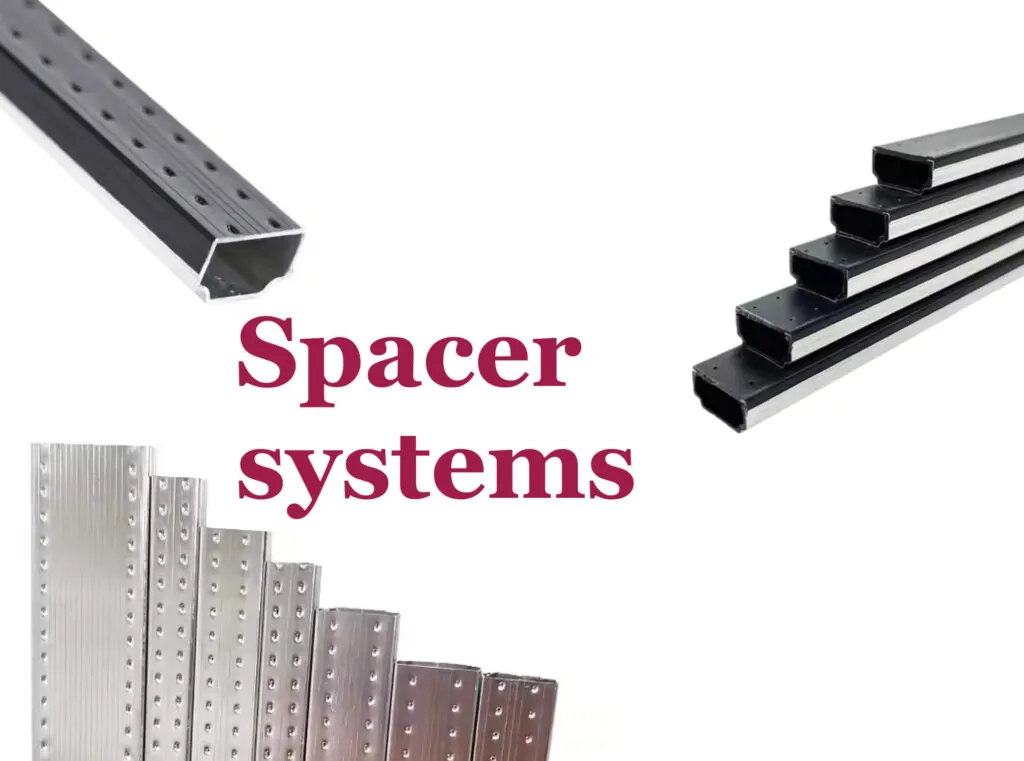
Types of spacers:
- Aluminium spacers: Traditionally, aluminium was commonly used due to its strength, but it is highly conductive, leading to thermal bridging (heat transfer around the edges), which reduces the overall efficiency of the glazing.
- Warm edge spacers: Modern spacers, known as warm edge spacers, are made from stainless steel, foam, or composite polymers. These spacers significantly reduce heat transfer around the edges, improving the overall U-value of the window.

Functions of spacers:
- Maintain cavity width: Spacers ensure the glass panes are held at the correct distance, which is essential for optimising insulation performance.
- Seal the edges: Spacers help seal the unit, preventing moisture from entering and ensuring the insulating gas (like argon or krypton) remains trapped within the cavity.
- Reduce condensation: By minimising heat transfer at the edges, warm edge spacers help reduce the condensation, that typically occurs around window edges where heat loss is greater.
Sealant in insulated glass units
The sealant plays a crucial role in maintaining the integrity of the glass unit ensuring that the spacer and glass panes are securely bonded, preventing gas leakage, and keeping out moisture.
The Primary sealants, typically made from butyl, create an airtight seal around the spacer to prevent gas leakage, while secondary sealants, such as silicone, polysulphide, or polyurethane, provide structural support, moisture resistance, and protection against environmental factors.
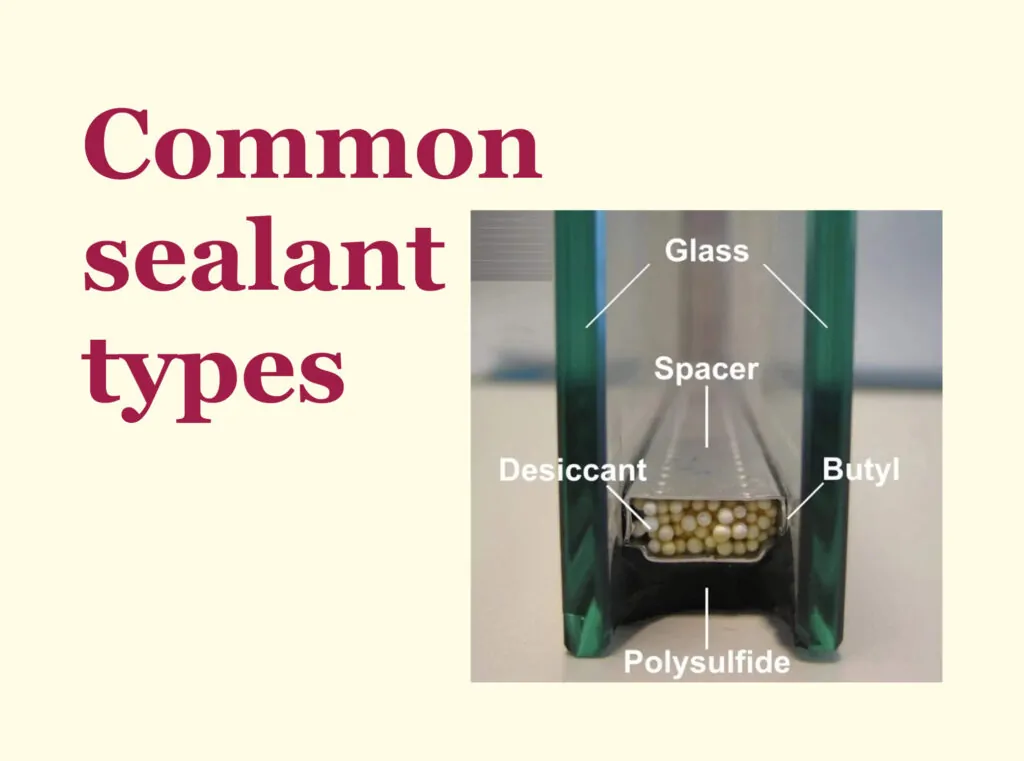
Together, these sealants ensure the long-term durability and optimal insulation performance of the IGU.
Functions and key characteristics of sealant in an IGU:
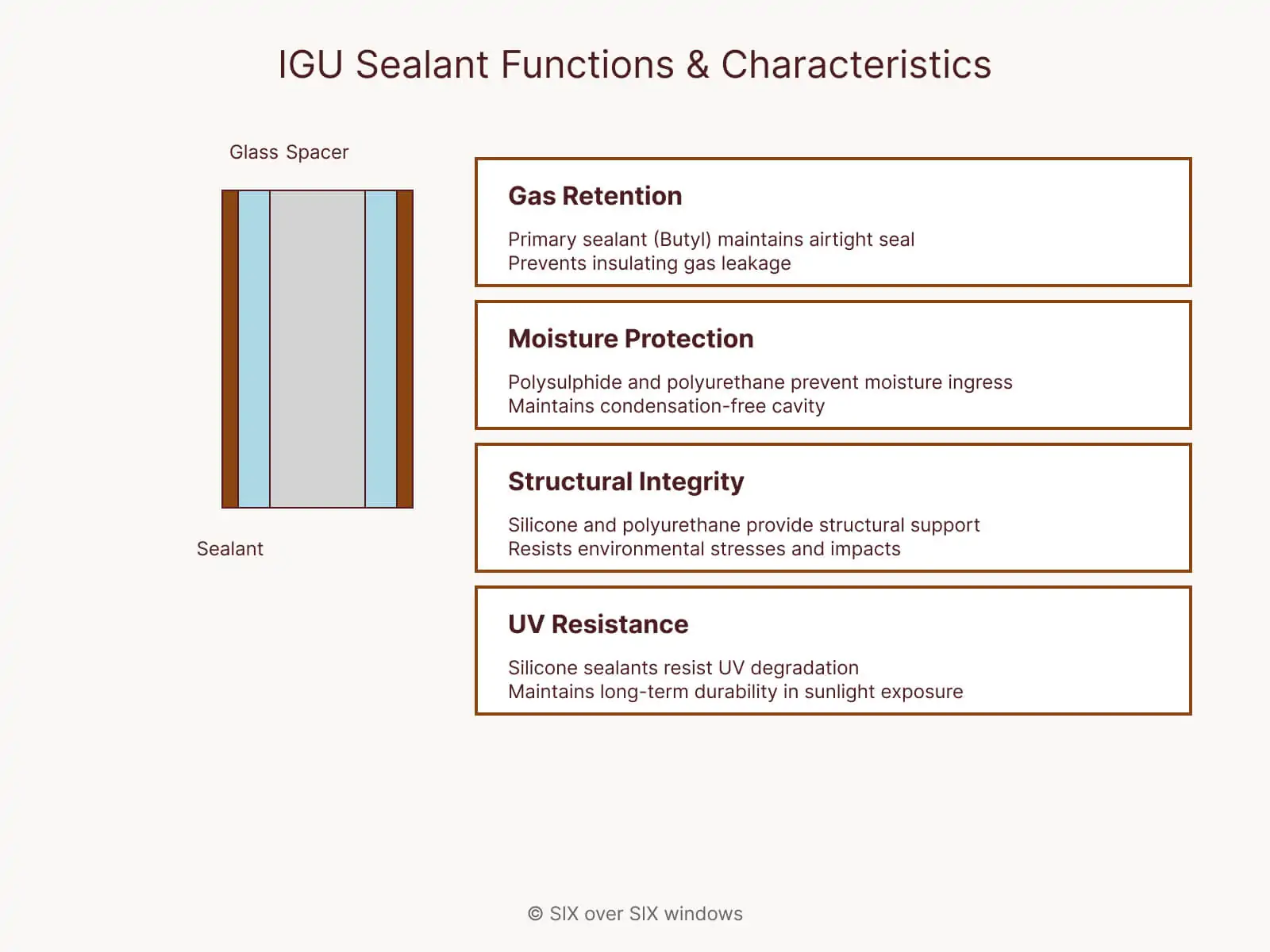
- Gas retention: The primary function of the sealant is to maintain an airtight seal around the edges of the glass unit, ensuring that the insulating gas (such as argon or krypton) remains trapped between the panes. Butyl sealants are particularly effective for this purpose, preventing gas leakage over time.
- Moisture protection: The sealant prevents external moisture from entering the cavity, which could cause condensation between the panes and reduce the unit’s thermal performance. Polysulphide and polyurethane sealants are highly resistant to water, ensuring the unit remains condensation-free.
- Structural integrity: Sealants bond the glass panes to the spacer, ensuring the structural stability of the IGU. This enhances the unit’s ability to endure environmental stresses, including pressure variations, temperature changes, and mechanical impacts. Silicone and polyurethane are commonly used as secondary sealants to provide this structural support, with silicone also offering strong resistance to UV radiation.
- UV resistance: Sealants, particularly silicone, are formulated to resist long-term exposure to sunlight without deteriorating, making them ideal for external sealing in environments with high UV exposure.
Common sealant types and their materials:
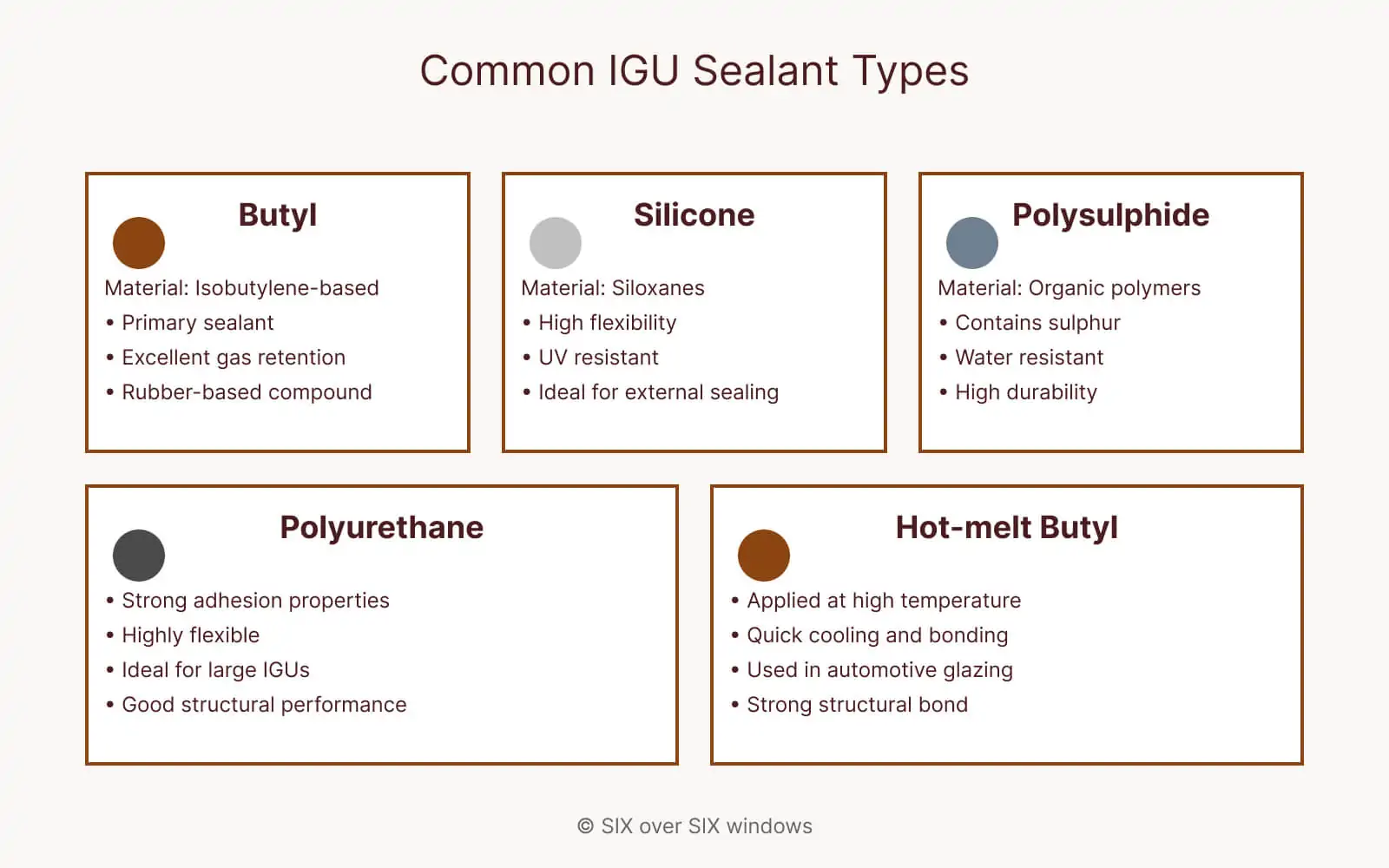
- Butyl: A rubber-based material made from isobutylene used as the primary sealant for gas retention.
- Silicone: Made from siloxanes, it offers flexibility, UV resistance, and is ideal for external sealing.
- Polysulphide: Composed of organic polymers containing sulphur for excellent water resistance and durability.
- Polyurethane: Known for its strong adhesion and flexibility, suitable for large or structurally demanding IGUs.
- Hot-melt butyl: Used in automotive or commercial glazing applications, applied hot and quickly cools to form a strong bond.
Cavity contents
The cavity between the glass panes in an insulated glazing unit is a key element in its insulating performance.
Originally, these cavities were filled with air. Air-filled cavities provide basic insulation but are less effective at reducing heat transfer than gas-filled units.
Gas fillings, such as argon, krypton, and xenon, are much denser than air, allowing them to be more effective at energy saving.
Using gas fillings in the insulated glazing unit cavity increases insulating properties, lowering the U-value and improving energy efficiency.
Types of glazing insulators: air, gas, vacuum
The thermal efficiency of insulated glass largely depends on the material used to fill the cavity between the panes. These cavities can be filled with air, gas, or a vacuum, each providing different levels of insulation.
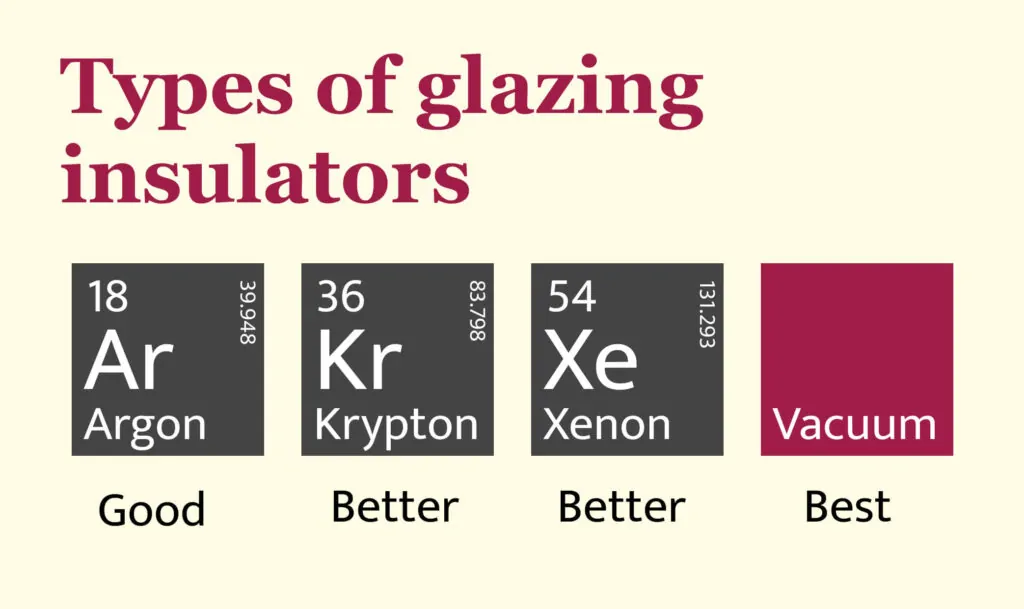
Air-filled insulated glass
Air-filled insulated glass provides basic insulation, but its performance is lower compared to gas or vacuum-filled options.
Due to the higher rate of heat transfer, air-insulated units do not provide the same level of thermal efficiency as more advanced technologies.
Gas-filled units
Gas-insulated units use denser gases than air, providing better thermal insulation. The most common gases used in these units are argon, krypton, and xenon, each offering different levels of efficiency and cost.
- Argon is the most commonly used gas for double and triple glazing. It is 34% denser than air and provides a significant insulation improvement at a relatively low cost.
- Krypton being denser than argon, offers superior thermal performance, making it ideal for tighter spaces in triple glazing, although it comes at a higher cost.
- Xenon is primarily utilised in high-performance or commercial glazing applications because of its excellent insulating properties, though its higher cost limits its use in standard residential settings.
However, every gas-insulated glazing unit eventually becomes air-insulated as the gas escapes through tiny leaks in the seals.
Over time the seals weaken, and the cavity becomes filled with air, resulting in reduced thermal performance.
Regular maintenance can help identify seal failures early, such as through condensation or fogging between the panes.
Vacuum insulated glazing units – a new generation of insulated glazing
Vacuum insulated glass (VIG) is one of the most advanced technologies in window insulation. It offers exceptional thermal performance with U-values of just 0.4-0.7 W/m²K.
VIG consists of two sheets of glass separated by a narrow vacuum gap, which eliminates heat transfer by conduction and convection.
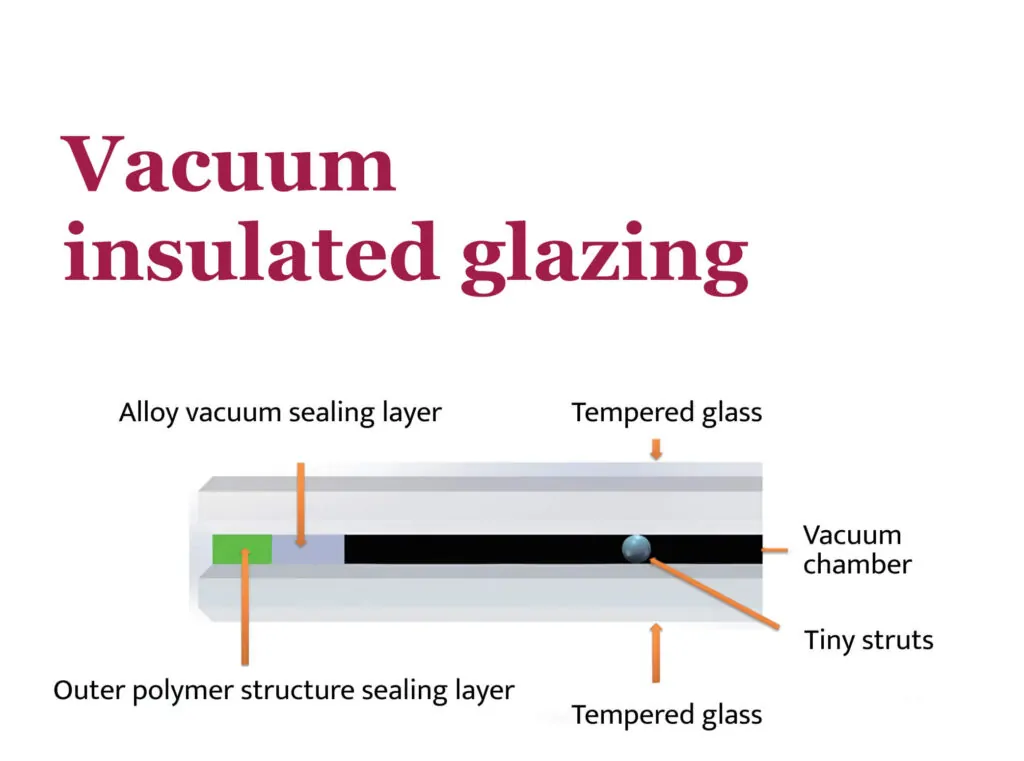
Vacuum glass units are much thinner than traditional double or triple glazing, typically around 6-12mm, making them ideal for retrofitting in listed buildings and heritage properties, where maintaining the original appearance is crucial.
In addition to improved thermal efficiency, VIG also provides excellent acoustic performance, making it suitable for urban areas where external noise is an issue.
Modern brands such as Fineo and LandVac are leading the way in VIG units nowadays.
These products offer superior insulation but they last for decades with warranties of 20 years or more.
The combination of durability, high performance, and a slim profile makes VIG a highly effective solution for those looking to maximise energy efficiency and comfort in their homes, especially in properties with limited window space.
Comparison of different types of insulated glass
The table below provides a comparison of different glass configurations, including double, triple, and vacuum-insulated glazing.
Glazing configuration | Number of panes | Cavity insulation | U-Value range (W/m²K) | Average thickness (mm) | Noise reduction (dB) | Light transmittance (%) |
Double Glazing | 2 | Air or gas-filled (argon/krypton) | 1.2 – 3.0 | 24 – 28 mm | 30 – 35 dB | 70 – 80% |
Triple Glazing | 3 | Gas-filled (argon/krypton) | 0.6 – 1.0 | 36 – 44 mm | 35 – 40 dB | 60 – 70% |
Different Cavity Variations | 2-3 | Wider cavity, gas-filled (argon/krypton) | Varies based on gas and cavity width | 28 – 48 mm | 35 – 42 dB | 60 – 75% |
Vacuum Insulated Glazing (VIG) | 2 | Vacuum-sealed gap | 0.4 – 0.7 | 6 – 12 mm | 36 – 40 dB | 75 – 85% |
FAQ
What level of energy savings can I achieve with insulated glass?
The energy savings you can achieve with insulated glass depend on factors such as the type of glazing (double, triple, or vacuum insulated), the quality of the installation, and the overall insulation of the building. Switching from single glazing to double glazing may help to reduce heat loss by up to 50%. Triple glazing or vacuum insulated glazing (VIG) can further enhance savings, particularly in colder climates. Homeowners typically see annual energy savings between £100 and £150 with double glazing, with higher savings possible with more advanced glazing systems.
Can insulated glass be used in sash windows?
Yes, you can use insulated glass in sash windows. Modern advancements, such as slim-profile double glazing and vacuum insulated glazing (VIG), allow insulated glass to be retrofitted into traditional sash windows without changing the original aesthetic. This is particularly useful for listed buildings or heritage properties, where maintaining the original character of the windows is of great importance. Insulated glazing improves thermal and acoustic insulation in sash windows while preserving their historic look.
How long do insulated glass units last?
Insulating glass units (IGUs) typically last between 15 and 25 years, which can vary based on the quality of the materials, the installation technique, and the surrounding environmental factors. Over time, the seals around the glass can degrade, leading to gas leaks or condensation between the panes, which reduces the unit’s insulating properties. Regular maintenance, such as checking for fogging or condensation, can help extend the lifespan of the glass. Some high-quality IGUs, particularly those from reputable manufacturers, may last even longer with proper care.
Are insulated glass and double pane glass the same?
Although people often use the terms “insulated glass” and “double pane glass” interchangeably, they have distinct meanings. Double pane glass refers specifically to glass units with two panes of glass, typically separated by a spacer and a cavity filled with air or gas. Insulated glass is a broader term that can refer to any multi-pane glass unit (including double, triple, or vacuum-sealed glazing) designed to improve thermal insulation.